Plasma cleaning is a process of using plasma energy to clean and modify the surface of a substrate like a circuit board assembly.
It is a highly effective surface cleaning and treatment process before application of conformal coatings and is gaining more popularity due its highly effective performance.
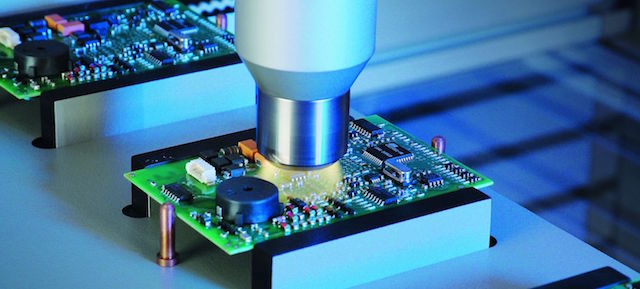
What is Plasma?
Plasma is the energy-rich gas state (also known as the fourth state of matter) that can be used to modify the surface of a product to improve its performance.
Plasma technology is based on a simple physical principle.
Matter changes its state when energy is supplied to it. Solids become liquid. Liquids become gas.
If additional energy is then fed into a gas by means of electrical discharge it eventually ionises and goes into the energy-rich plasma state, plasma is created.
This modification can be improving the adhesion of a conformal coating or change the surface characteristics of the board.
How is Plasma used for improving the performance of coatings with printed circuit boards?
For electronic circuit surfaces, plasma treatment can be used in two highly effective ways.
That is it can:
- Clean the surface of the circuit board. The surface will be free of residues and 100% contamination free including release agents and additives.
- Activate the surface of the circuit board assembly. This will allow easier bonding and better adhesion of conformal coatings.
These properties make it an interesting technique for improving the surface performance of an electronic circuit board.
In fact, plasma treatment can clean, activate or coat nearly all surfaces. These surfaces include plastics, metals, (e.g., aluminum), glass, recycled materials and composite materials.
This means the plasma process can be highly effective on many different products.
For electronic circuits, plasma treatment can be used in two highly effective ways. First, it can clean the surface of the circuit board. Second, it can activate the surface of the circuit board assembly to allow easier bonding and better adhesion of conformal coatings and materials like Parylene.
What are the typical plasma processes available for surface treatment?
There are traditionally three types of plasma treatment:
- Low-pressure plasma
- Corona treatment
- Atmospheric pressure plasma
Low-pressure plasma
These plasmas are generated in closed chambers in a vacuum (10-3 to 10-9 bar).
They can be used in conjunction with Chemical Vapor Deposition (CVD) coatings like Parylene before application.
Corona treatment
Corona treatment (corona process) is a physical process involving high voltage and is mainly used for treatment of films.
This is normally not suitable for electronic circuit boards.
How is the plasma applied to a circuit board to clean and activate the surface?
For materials like liquid conformal coatings then atmospheric pressure plasma is an excellent process for cleaning surfaces and improving adhesion and surface energy performance of circuit boards for conformal coatings.
Atmospheric plasma is generated under normal pressure. This means that low-pressure chambers are not required.
The plasma is created with clean and dry compressed air and does not require forming gases. It is possible to integrate plasma directly into manufacturing processes under normal pressure conditions.
Typical plasma components used for cleaning surfaces on circuits are:
- Plasma jets (nozzles) to apply the plasma to the surface of the circuit board. They could be controlled by a robotic system.
- The plasma generators that create the plasma to clean or supply the coatings as required. They provide output power and, in conjunction with complete pretreatment stations, assume various control functions.
- The process monitoring that controls the nozzles, the movement of the system and the quality of the output.
These three parts form the plasma cleaning process.
For Chemical Vapor Deposition (CVD) coatings like Parylene then low-pressure plasma can be used in the chamber before application.
These plasmas are generated in closed chambers in a vacuum (10-3 to 10-9 bar).
Want to know more about plasma cleaning and conformal coating performance?
Contact us now to discuss what we can offer you in terms of cleaning fluids from our Surclean range of materials.
Give us a call at (+44) 1226 249019 or email your inquiries at sales@schservices.com